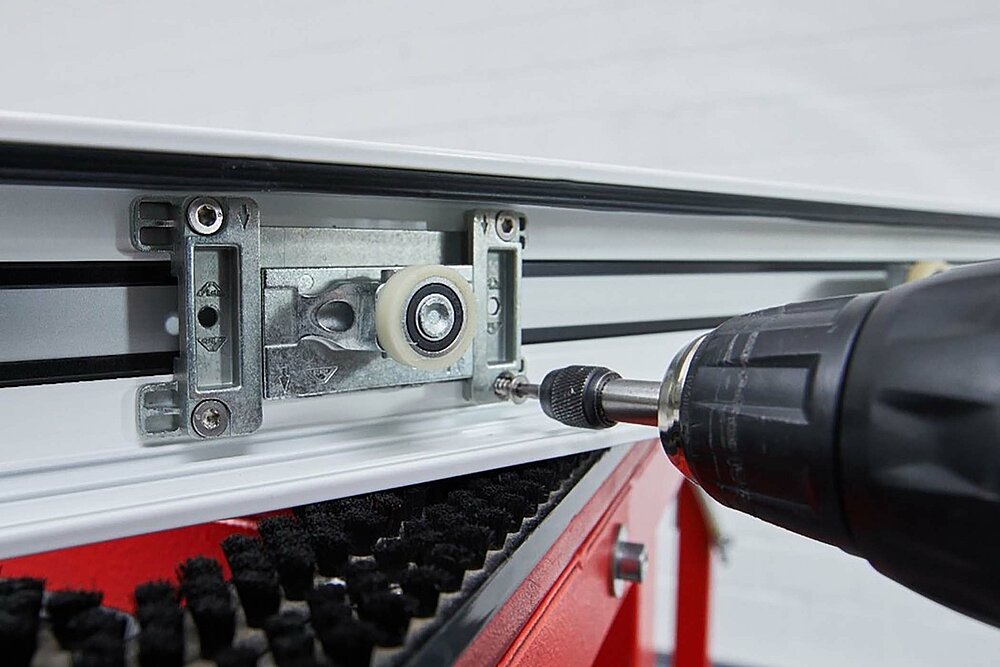
“A good partner thinks ahead”
Roto Window and Door Technology focuses on ease of installation to ensure economical manufacturing of building elements / Streamlined processes thanks to identical parts / Customised hardware technology without “Bypass” production lines / Saving time: new mounting concepts, prefabrication and modular systems / Plug&Play for electronic components / Seals and glazing technology for quick and reliable installation
Leinfelden-Echterdingen – How can we save time in window and door production? Building element manufacturers ask themselves this question on a regular basis. This is also a key question for component manufacturers, since hardware, sealing profiles and glazing blocks designed for ease of installation also provide benefits in terms of efficiency for window and door production.
Read more
Roto has a reputation among window and door manufacturers as an interesting partner for discussions about process optimisation. “We have been working closely with many customers for decades now to continuously improve efficiency throughout the entire value chain,” confirms Eberhard Mammel, Director of Marketing and Product Innovation at Roto Frank Fenster- und Türtechnologie GmbH. However, the fact that Roto has designed its own products from the outset to be particularly easy to install is just as important as process consulting. This feature is considered and incorporated right from the start of a development process. “We systematically design our hardware, sealing profiles and glazing methods to incorporate ease of installation.”
Standardising processes
Roto gives equal consideration to manual, semi-automated and fully automated production for processing each of its products. How does a piece of hardware need to be designed to ensure that the least possible routing, drilling and screwdriving work is required to install it? How can we avoid the need to remove a building element from the standard process if an end customer has selected a comfort solution and integrated additional components? “Roto designers put a lot of effort into ensuring that our customers have an easier time later on,” summarises Kevin Bienert, Head of Project Management Office, Standards & Data Management. Roto also feels a shared responsibility for IT costs. “Each additional component results in cost and effort for programming the process and plant control system. Therefore, the fewer components we need in order to provide varied solutions and wide application ranges, the better.”
Increasing number of identical parts
A Roto hardware component should be able to be used with maximum flexibility and processed quickly and reliably, summarises Bienert. This is because utilisation of identical parts plays a central role in ensuring production efficiency in a world of complex products and individual requirements for windows and doors. The design of “Roto NX” represents a major step in terms of increased efficiency. Many components developed for this Tilt&Turn hardware, such as the corner drive, are now found in other Roto window, door and sliding hardware products. The central locking systems of the “Roto Patio Inowa” and “Roto Patio Alversa” sliding hardware systems, for example, are likewise identical to those in the “Roto NX” range. Bienert cites a further example of the identical parts strategy in the “Roto Safe” range. Identical frame components can be combined with one of five different additional lock options as required. A further efficiency increase: “The routing in the sash is always the same for all locks.” Standardisation efforts such as these are a mandatory part of the work of Roto designers, but the results are well worth it.
Flexible manufacturing on one production line
“Our task is to establish product ranges that enable users to flexibly meet different end customer requirements on a single production line,” Mammel states. In order to ensure error-free and efficient installation, it is important that even elements equipped with additional comfort or security components do not need to be taken out of the production line. Only slight variations to the manufacturing process are acceptable. One example of components designed in this way: the “SoftOpen” and “SoftClose” comfort functions of the “Patio Inowa” sliding hardware are integrated into the control unit. This means that the production process only deviates slightly from the standard.
Another prominent example from the Roto sliding hardware range is “Patio Alversa”. This system combines a Tilt&Slide solution and three Parallel Sliding solutions, including various ventilation functions. The roller units, sliding scissor stays and track sets can be used for multiple versions. This means greater standardisation and fewer parts, which significantly reduces storage and logistics costs. The modular system design makes it possible to produce all four variants of the “Roto Patio Alversa” on a single production line.
If windows and doors are integrated into an electronic monitoring system, for example, this would only entail a small amount of additional work in production, Bienert emphasises, as Roto works with concealed magnets. The “E-Tec Control MVS” contact elements for electronic locking monitoring are positioned under a locking point. No locking points are wasted and the standard configuration of the window is retained – which is important for production management. “The contacts are put into place without needing to deviate from the standard process on the production line,” Bienert states. The same applies for Tilt&Turn solutions with added value: regardless of whether the technology is ‘TiltSafe’ or ‘TiltFirst’, the alternative or additional components are integrated into the standard process. ‘Bypass’ production lines are not required.”
Fewer screws used – which saves time
A few more Roto developments save time directly: the “Clip&Fit” design of the “Roto NX” components with form-fitting connections enables the hardware to be clamped into the sash with no need for a screw fixing, for example, and ensures that it does not slip out of place when transferring it to another workstation. The “Roto Patio Inowa” sliding hardware is likewise designed to save time in processing. Its components such as the roller unit, control unit, mullion and centre lock have a reduced number of screw-fixing points. Particularly practical: the centre fixing triggers automatically when it is screwed in.
Users of the “Roto AL Designo STS”, a concealed Tilt&Turn hardware solution that is also suitable for aluminium profiles installed flush with the surface, benefit from a special mounting concept for the sash stay and pivot rest. They are fixed in place with mounting wedges. There is no need for a punched hole in the groove base.
Efficient production of main doors
Roto offers another clever mounting solution for manufacturers of aluminium doors: the “224 A” and “324 A” butt hinges from the “Roto Solid B” product range are fixed in place with clamping blocks on the sash hinge and a clamping plate on the frame hinge. The profile does not need to be processed. Another advantage: Roto adjusts the level of preassembly to meet the individual requirements of each door manufacturer. For example, the clamping blocks can come preassembled. This additionally speeds up installation. The mounting concept of the aluminium butt hinges also can be flexibly adapted to the system-specific groove of a profile. This is how individual hinge versions tailored to the individual system are created with the same basic concept. Regardless of the frame material, working with “Roto Solid B” butt hinges provides installers with time savings when joining the leaf and frame as well as on the building site. This is because the integrated continuous height and lateral adjustment, which can be used even when closed, eliminates the need to unhinge the leaf.
Modular systems
“Roto offers a balance between factory preassembly and modular system solutions,” emphasises Eberhard Mammel. To ensure that door manufacturers can achieve flexible production with efficient component storage, Roto has most recently developed the “Tandeo Upgrade-Kit”, for example. This can be used to expand a “Tandeo” multipoint lock to include a drive unit as required, if the option for electronic door opening is requested. “For manufacturers that sell many electronically opening doors, Roto also offers the ‘Eneo A’ preassembled electromechanical locks as part of our product range,” adds Kevin Bienert.
Fabricators of the “Roto NX” also benefit from the concept of modular product design. The manufacturer refers to this as the “Easy-Mix system”: gearboxes and lock casings are supplied separately from the faceplate. This enables the fabricator to flexibly select the gearbox they require and install it without needing to use screws. An additional lock casing is only integrated if required.
Electromechanical drives with Plug&Play
Roto offers the “Tandeo Upgrade-Kit” with the feature it calls the “Plug&Play connection”, which makes installation much simpler. The “Roto Safe E | Eneo CC” and “Roto Safe P | Eneo CF” electromechanical multipoint locks for escape doors also feature this proven technology. “Thanks to Plug&Play, installing the locks as well as our ‘4in1’ access control system into doors is as easy as connecting a PC to a printer via a cable,” Bienert describes.
The “4in1” access control system is a control panel for electromechanical locks that combines four opening methods in one component. The door can be opened by typing a numerical code directly on the panel. Alternatively, it can be opened via a finger scan on the panel, or via an RFID-compatible medium such as a chip, or via Bluetooth using a smartphone. “This is another example of our efforts to reduce inventory requirements for our customers,” Bienert emphasises. “A single component enables electromechanical door opening via four different operating modes.”
Roto offers the “E-Tec Drive” with Plug&Play technology for windows and fanlights that feature electromechanical opening. “Roto designers want to make it easy for window and door manufacturers to integrate electromechanical drives. In doing so, they ensure that windows and doors with particularly high operating convenience can be installed almost as easily as standard windows,” Mammel states.
Glazing and seal technology optimised for installation
Simply insert it, and you’re done. A glazing block that performs its function without slipping makes work easier for installers. Roto is well aware of this, and provides powerful assistance in its “Roto Glas-Tec” range. Two examples feature in the discussion: the manufacturer’s compensating blocks create a level surface for glazing blocks in PVC windows, and can be clipped into the glass rebate. Thanks to their excellent grip, they can be used early in the sash installation process, long before glazing. Example 2: the “GL-B” glazing block with two brake membranes that prevent the block slipping or falling down in the glass rebate if installed vertically.
Sealing profiles optimised for installation likewise measurably save time. Jürgen Daub, Head of Research and Development at Deventer, explains what matters: “We design our sealing profiles with a particularly firm ‘spine’, which enables them to be clicked into place rather than pressed into place. Components such as the S 7503b seal, which is in high demand among timber window manufacturers, can be simply pulled into place using a finger.” They are manufactured using the material TPE, which retains its shape excellently and is particularly durable, resulting in longer window maintenance intervals.
Daub also considers the Deventer “Master Corner” TPE profile, which is suitable for windows made with any frame materials, to be truly revolutionary for economical installation. The special features of its profile geometry are striking: a hard profile leg at an angle prevents the sealing profile from rolling up in the corner. It precisely counters the force generated by positioning. A combination of rigid and flexible TPE minimises rolling up on the inside. This enables the “Master Corner” to be easily guided around corners. No cutting, no welding. “This saves time and therefore costs, and also prevents the seal from hardening in the corner under the effect of heat produced by welding PVC profiles,” Daub explains. As the foot of the “Master Corner” seal is fitted with a slide lining, it can be easily inserted into aluminium profiles without using aids.
The North American company Ultrafab Inc., which has also been part of Roto Window and Door Technology since December 2022, supplies customers with advanced stack insertion devices along with sealing profiles developed specifically for their requirements. These assist with pulling the seal into the window profiles. A service that is the only one of its kind in the industry. Each device is configured according to customer requirements and can mount different Ultrafab seals. T-groove seals are pulled into a PVC or aluminium profile at a speed of up to 6 feet (approx. 2 metres) per second. Since Ultrafab was founded in 1970, this family company has evolved into an established technological leader in the processing of thermoplastic PVCs. Its product range includes high-quality brush seals and extruded sealing profiles for building elements.
“Providing installers with the opportunity to work quickly and error-free by selecting easy-to-install components and good tools increases production efficiency,” summarises Mammel. Roto provides additional opportunities for streamlining by implementing modular product range structures. “A large number of identical parts reduces costs for our customers – from the supply stage, to delivery, through to transportation to the installation table – which they very much appreciate.”
Hard work to ensure easy installation
For almost 90 years, Roto has operated as a company of inventors that thinks and designs for industrial production customers, Mammel emphasises in conclusion. This is intended to provide window and door manufacturers with ideal support for producing building elements both flexibly and economically. “Developing easy-to-install components and economically manageable product ranges is and will remain our core competency. As a good partner, Roto thinks ahead and considers those who will process our hardware, seals and glazing products.”